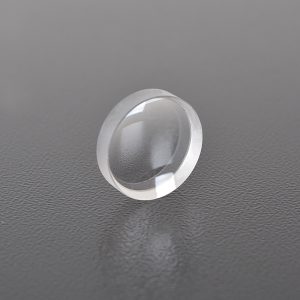
High-precision Lens Processing for Astronomical Telescopes
As an important tool for human exploration of the universe, the quality of the core component of the astronomical telescope, the lens, directly determines the imaging effect of the telescope. Lens processing is a key link in optical manufacturing, involving multiple processes from raw material selection to precision processing. This article will introduce the processing process of telescope lenses in detail to help readers understand the principles behind this precision technology.
1. Selection of lens materials
The materials of telescope lenses are usually optical glass or special crystals, such as quartz, calcium fluoride, etc. These materials need to have the following characteristics:
1. High transmittance: The lens material needs to have a high transmittance in the visible light, infrared, ultraviolet and other bands to ensure that light can pass efficiently.
2. Low dispersion: Dispersion refers to the separation phenomenon of light of different wavelengths when passing through the material. Low dispersion materials can reduce chromatic aberration and improve imaging quality.
3. Thermal stability: The lens should not produce obvious deformation or refractive index changes when the temperature changes to ensure the stability of the telescope in different environments.
4. Mechanical strength: The lens needs to have a certain hardness and impact resistance to cope with mechanical stress during transportation and use.
2. Rough processing of lenses
In the first step of lens processing, the raw material will be cut into a blank close to the final shape. This process usually uses diamond cutting tools to ensure the flatness and dimensional accuracy of the cut surface. The goal of rough processing is to lay the foundation for subsequent precision processing and reduce the processing volume of subsequent processes.
3. Precision grinding of lenses
Precision grinding is one of the most critical steps in lens processing. Through grinding, the surface of the lens gradually approaches the curvature and shape required by the design. The grinding process is usually divided into the following stages:
1. Rough grinding: Use coarser abrasives to quickly remove excess material so that the surface of the lens is initially close to the design shape.
2. Medium grinding: Use medium-sized abrasives to further correct the shape of the lens surface and reduce surface roughness.
3. Fine grinding: Use fine abrasives to make the lens surface reach a higher degree of flatness and finish, in preparation for subsequent polishing.
During the grinding process, the curvature of the lens is precisely controlled by a computer-controlled grinder to ensure that the geometry of the lens meets the design requirements.
4. Polishing of lenses
Polishing is the last step in lens processing, and its purpose is to remove tiny scratches produced during the grinding process and make the lens surface reach optical level smoothness. Polishing usually uses polishing powder and polishing pads to make the lens surface reach nanometer level flatness through mechanical or chemical action.
During the polishing process, the surface shape and curvature of the lens need to be strictly monitored to ensure that it meets the design requirements. In modern polishing technology, computer-controlled polishing machines can automatically adjust polishing parameters according to real-time detection data to ensure the high precision of the lens.
5. Coating of lenses
In order to improve the transmittance of the lens and reduce reflection loss, the surface of the lens usually needs to be coated with one or more layers of optical thin film. The selection and thickness of the coating material need to be optimized according to the use band and design requirements of the lens. Common coating materials include magnesium fluoride, silicon dioxide, etc.
The coating process is usually carried out in a vacuum environment, and the film is evenly deposited on the surface of the lens through physical vapor deposition (PVD) or chemical vapor deposition (CVD) technology. The coated lens not only has higher light transmittance, but also effectively reduces glare and ghosting, and improves imaging quality.
6. Lens inspection and correction
After the lens is processed, it needs to be strictly inspected to ensure that its optical performance meets the design requirements. Common inspection items include:
1. Surface shape inspection: Use an interferometer or profilometer to detect the curvature and shape error of the lens surface.
2. Surface roughness inspection: Use an atomic force microscope or white light interferometer to detect the microscopic roughness of the lens surface.
3. Transmittance inspection: Use a spectrophotometer to detect the transmittance of the lens in different bands.
4. Coating quality inspection: Use an ellipsometer or reflectometer to detect the thickness and uniformity of the coating.
If errors are found in the lens during the inspection, they can be corrected by local polishing or re-coating until the lens meets the design requirements.
7. Assembly and debugging of the lens
After the lens is processed, it needs to be assembled into the optical system of the telescope. During the assembly process, the position and angle of the lens need to be precisely adjusted to ensure the alignment of the optical axis and the imaging quality. After the assembly is completed, the overall debugging is also required to ensure that the optical performance of the telescope is in the best state.
Conclusion
Telescope lens processing is a highly sophisticated technology that involves knowledge in multiple fields such as material science, mechanical processing, and optical design. Through strict processing procedures and quality control, modern telescope lenses can achieve extremely high optical performance, providing a powerful tool for human exploration of the universe. With the continuous advancement of technology, the processing accuracy and performance of telescope lenses will be further improved in the future, bringing more breakthroughs to astronomy and space exploration.
Hanzhong Brisun Optics Co., Ltd. Is the high precision optical element manufacturer provides customized production of Various optical lenses, including spherical lens, cylindrical lens, optical window, mirror, prism, filter, metal base mirror and other high-precision optical elements. The base materials include various optical glass, fused quartz, calcium fluoride (CaF2), zinc selenide (ZnSe), germanium (GE), silicon (SI), sapphire, metal and other materials. And provide antireflective film, high reflection film, spectroscopic film, metal film and other optical coatings.
Welcome to OEM and Purchasing!