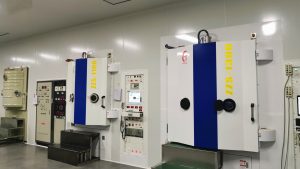
Quality Control: The Key to Ensuring Product and Service Excellence
In today’s highly competitive market environment, in addition to innovation and marketing strategies, the stability and reliability of product quality are also crucial for companies to stand out from their competitors. Quality control (QC), as a core component of the quality management system, runs through every link of product design, production, delivery and after-sales service. This article will explore the concept, importance, main methods and implementation steps of quality control in depth to help companies better understand and apply quality control to improve the overall quality of products and services.
1. The Concept of Quality Control
Quality control refers to a series of systematic activities to ensure that products or services meet established quality standards and requirements. Its core goal is to reduce defects and improve product consistency and reliability by preventing, detecting and correcting problems in the production process. Quality control is not just a link in the production process, but a continuous improvement process throughout the entire product life cycle.
2. The Importance of Quality Control
1. Improve customer satisfaction
High-quality products and services can meet or even exceed customer expectations, thereby improving customer satisfaction and loyalty. Improved customer satisfaction not only helps companies establish a good brand image, but also brings more repeat customers and word-of-mouth communication.
2. Reduce production costs
Through effective quality control, companies can promptly discover and correct problems during the production process, reduce the cost of rework, scrap and after-sales maintenance. This can not only improve production efficiency, but also reduce the company’s operating costs.
3. Enhance market competitiveness
In the global market, product quality is an important manifestation of corporate competitiveness. Through strict quality control, companies can ensure product consistency and reliability, thereby occupying an advantageous position in the fierce market competition.
4. Compliance with regulatory requirements
Many industries have strict quality standards and regulatory requirements, such as food, medicine, and automobiles. By implementing quality control, companies can ensure that their products comply with relevant regulations and avoid legal risks due to quality issues.
3. Main methods of quality control
1. Statistical process control (SPC)
Statistical process control is a method of monitoring and controlling the production process through statistical analysis. By collecting and analyzing data in the production process, companies can promptly detect abnormal fluctuations in production and take corresponding measures to adjust to ensure the stability of product quality.
2. Total quality management (TQM)
Total quality management is a customer-centric, all-involved quality management method. It emphasizes continuous improvement of product and service quality through continuous improvement and full participation. TQM not only focuses on quality control in the production process, but also covers various links such as design, procurement, and sales.
3. Six Sigma
Six Sigma is a data-driven quality management method that aims to reduce the defect rate to 3.4 parts per million by reducing variation in the production process. Six Sigma helps companies solve quality problems systematically through the DMAIC (Define, Measure, Analyze, Improve, Control) process.
4. Quality Function Deployment (QFD)
Quality Function Deployment is a method of converting customer needs into product design and production requirements. Through QFD, companies can ensure that product design meets customer needs, thereby controlling product quality at the source.
4. Implementation steps of quality control
1. Establish quality standards
Companies first need to establish clear quality standards based on customer needs, industry standards and regulatory requirements. These standards should include specific requirements for product performance, appearance, reliability, etc.
2. Establish quality control processes
After establishing quality standards, companies need to establish a complete set of quality control processes to clarify the responsibilities and operating specifications of each link. The quality control process should include raw material inspection, production process monitoring, finished product inspection and other links.
3. Train employees
The effective implementation of quality control is inseparable from the participation and cooperation of employees. Companies should regularly train employees on quality control to ensure that they have relevant knowledge and skills and can strictly implement quality control processes in actual work.
4. Monitoring and Improvement
Quality control is a process of continuous improvement. Enterprises should promptly discover problems in production through regular inspections and data analysis, and take corresponding improvement measures. At the same time, enterprises should also encourage employees to put forward improvement suggestions and continuously optimize the quality control process.
5. Future Development Trends of Quality Control
With the advancement of science and technology and changes in market demand, quality control is also constantly developing and innovating. In the future, quality control will rely more on emerging technologies such as big data, artificial intelligence and the Internet of Things. Through real-time data collection and analysis, enterprises can monitor the production process more accurately, predict potential quality problems, and take preventive measures. In addition, intelligent quality control equipment and technology will further improve production efficiency and product quality.
Conclusion
Quality control is the key for enterprises to ensure the excellence of products and services. By implementing effective quality control, enterprises can not only improve customer satisfaction and reduce production costs, but also enhance market competitiveness. In future development, enterprises should actively embrace new technologies and continuously innovate quality control methods to cope with the increasingly complex market environment and customer needs. Only by taking quality control as the core strategy of enterprise development can we be invincible in the fierce market competition.
Hanzhong Brisun Optics Co., Ltd. Is the high precision optical element manufacturer provides customized production of Various optical lenses, including spherical lens, cylindrical lens, optical window, mirror, prism, filter, metal base mirror and other high-precision optical elements. The base materials include various optical glass, fused quartz, calcium fluoride (CaF2), zinc selenide (ZnSe), germanium (GE), silicon (SI), sapphire, metal and other materials. And provide antireflective film, high reflection film, spectroscopic film, metal film and other optical coatings.
Welcome to OEM and Purchasing!